Ford invented proprietary weld techniques which proved worthy of being used in the production of the world’s best-selling truck. The weld tips need constant cooling in order to maintain continuous operation and FCS was tasked with engineering a complete custom process cooling system.
The Ford Motor Company has a long history of quality and innovation. It’s fitting they’ve become the first automaker to mass-produce a truck with an all-aluminum body. More specifically, a high-strength, military-grade aluminum alloy body that is joined to an all-new high-strength steel frame – making the truck 700 lbs lighter than its predecessor while adding strength, efficiency and improved performance.
Because no one has ever created a high-volume truck with an all-aluminum body, Ford had to develop all-new processes, technologies and standards, and make several upgrades at their Ford Dearborn plant, to ensure success. This included having to perfect heat treating and hydroforming techniques that were necessary to create the aluminum body. Additionally, Ford invented proprietary weld techniques which proved worthy of being used in the production of the world’s best-selling truck. Of course, welding creates heat – especially at this scale – which is where Fluid Cooling Systems (FCS) comes in. The weld tips need constant cooling in order to maintain continuous operation and FCS was tasked with engineering a complete custom process cooling system. This included equipment, pipe sizing, routing instrumentation, the control scheme and a few extras. FCS has been a trusted Ford supplier for several years and was honored to be part of such a historic milestone.

Complete integrated chilled water, heat transfer and precise controls for Ford Motor Company. FCS has enjoyed a long term relationship with Automotive customers. Ford Motor Company has many FCS Solutions, including a 5,200 ton system with seven outdoor modular buildings.
The first step in any successful project is to create a detailed schedule with all key milestones identified. The next step is to share it with all stakeholders to ensure everyone is on board with timing requirements
Once timing and expectations were solidified, the FCS team focused on providing the best, most complete solution for Ford. They made a couple of site visits to meet with Ford engineers, take measurements and work through updated requirements before and during the design stage. Communication was key. As changes occurred, the FCS team was able to adapt quickly and make any necessary design updates before they impacted the schedule.
The onsite measurements were vitally important not only to ensure piping dimensions and fit in the final footprint, but also to ensure there would be sufficient space in the rigging path from the truck to the final destination. In this case, the system design was broken into three skids to accommodate transporting requirements. Harting wire connectors were used for testing in shop prior to shipment and for easy assembly in the plant. This helped the production and installation teams save time and ensure proper wiring connections were made between the three skids.
FCS’s drawings were provided to Ford engineers and incorporated into their CAD program so they could verify system integration prior to build out. This smart step in the process saved planning and engineering time and helped to avoid any costly oversights by either team. FCS also provided a controls matrix to Ford so their maintenance staff would be familiar with all of the functions and alarms in the control panels.
The system was designed to a high standard to guarantee Ford the maximum amount of operations time. FCS included a backup plate and frame heat exchanger as well as backups for all pumps, providing 100% redundancy and allowing this equipment to be cycled on and off to reduce wear. This allows for preventative maintenance without shutting down the system. Additionally, the pipe diameter was sized based on water velocity to reduce the likelihood of pipe and component erosion. This also helped reduce the noise generated by the system’s fluid flow to help keep ambient noise levels down.
Free cooling was one of the main requirements on this project. It was accomplished by designing the heat exchanger to be used with either the chiller or cooling tower. During cooler months, the chiller can be shut down with the chilled water loop isolated, which allows the use of cold water provided through a closed circuit evaporative cooler. Colder seasonal temperatures chill the process water at a fraction of the cost of running a chiller. Ford maintenance staff can run through the chiller’s routine maintenance during the free cooling mode without shutting down production or compromising the quality of chilled water being sent to the process – all while saving energy and reducing the carbon footprint.
The Outcome
Because of their due diligence up front, constant communication and familiarity with Ford’s global requirements, FCS delivered everything on time and within budget. There were no surprises and no change-orders
Because free cooling was utilized, Ford can expect to save 88kw/hr when the system is operating in the free cooling mode. Based on planned operating schedules, this custom cooling system will pay for itself in approximately five years.
Ford ended up with an innovative industrial design that’s efficient and scalable for future expansion, and will be applied to other facilities in the near future.

Lastly, Fluid Cooling Systems was trusted to be an integral part of Ford’s new aluminum offering, and in the end proved once again to be up to the task presented by one of the world’s most recognized and enduring brands.

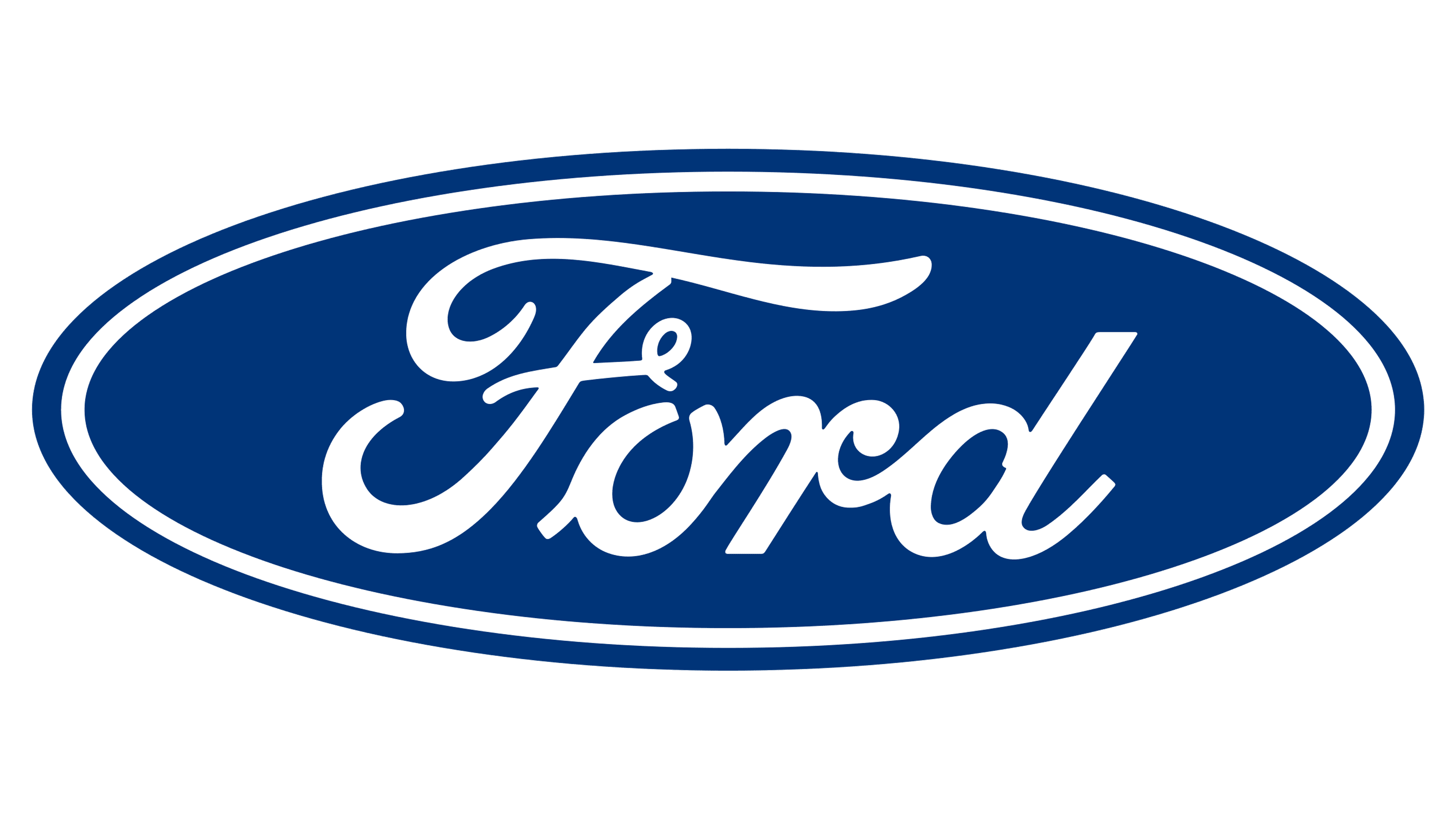
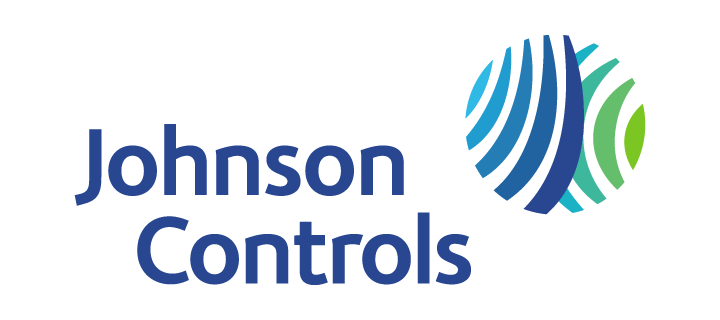


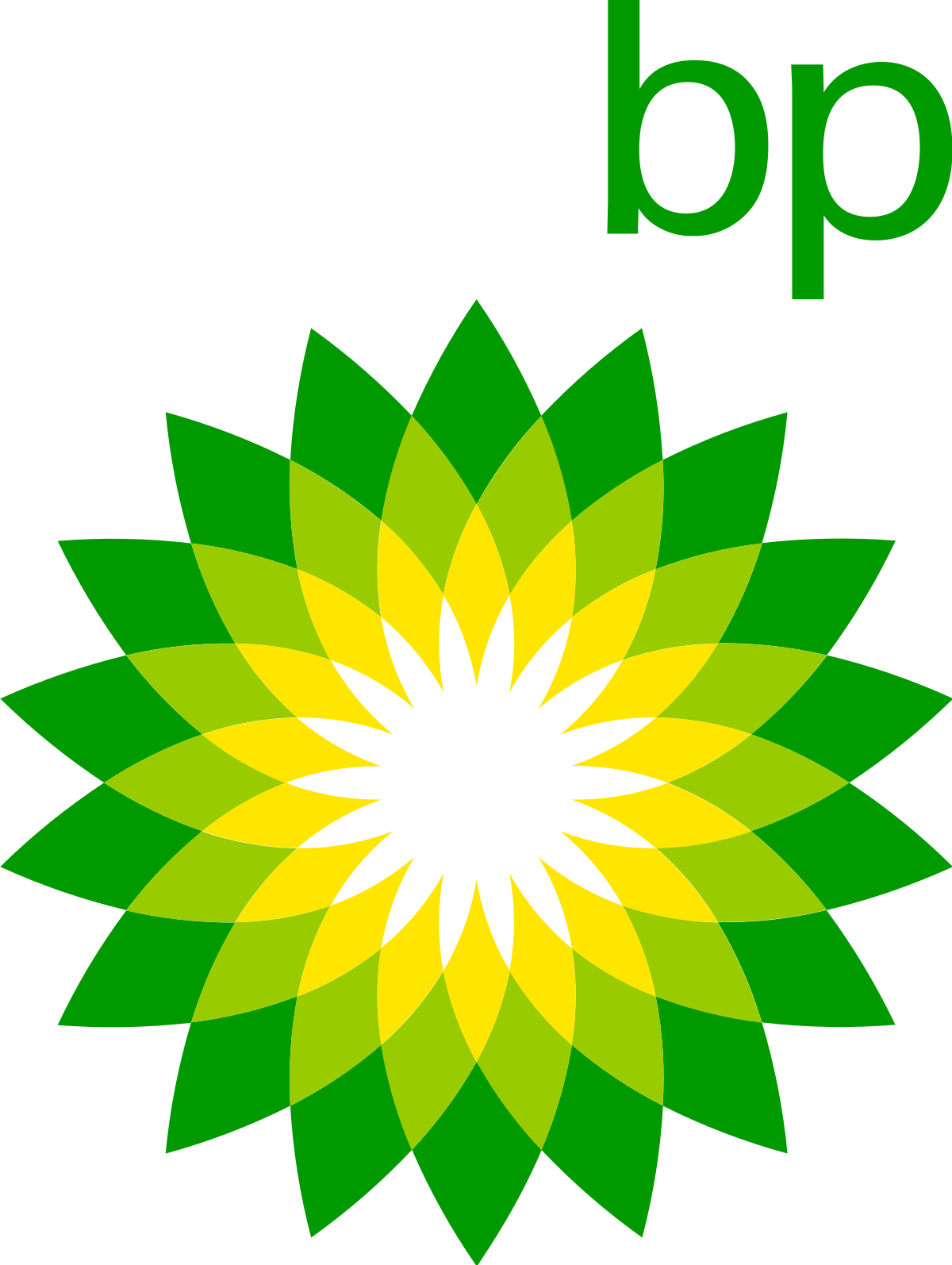